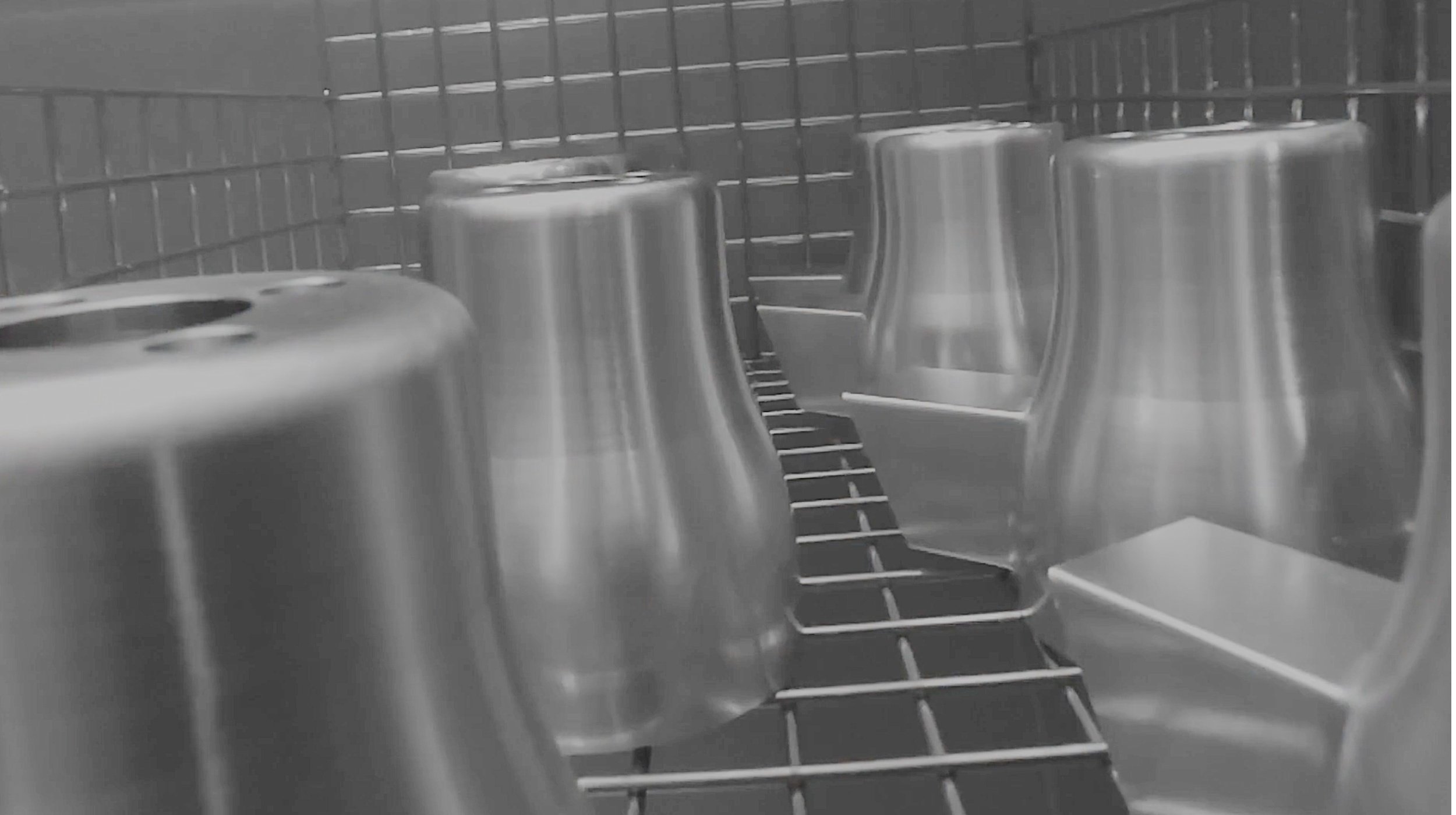
TiZr Passivation
Chrome Free Conversion Coating
What is TiZr passivation?
TiZr is shorthand for the titanium zirconium passivation process applied to aluminium components. This removes the natural oxide layer and replaces it with a stable, chemically modified ‘shield’ layer. Passivation is also referred to as conversion coating.
TiZr passivation creates a stable surface which will allow bonding and welding processes to deliver repeatable, strong, durable adhesive bonds. This conversion coating process also provides a stable base for powder coating and offers additional protection against corrosion. This is important in environments where the aluminium component may be exposed to moisture, chemicals, or high temperatures.
TiZr passivation and laser welding
TiZr is becoming increasingly popular as a pre-treatment for laser welding, the protective surface preventing unwanted oxidation around the weld zone. The clean, passivated surface promotes better laser absorption and a more consistent weld, reducing the risk of porosity, cracking, or defects in the weld seam.
Over 20 years’ experience in providing TiZr pre-treatments
As the first metal treatment provider in the UK to install TiZr as a chrome-free passivation process (since 2001), Powdertech Surface Science is the most experienced outsource TiZr pre-treatment provider in the country with an unrivalled body of knowledge. We use the latest Gardobond® systems for TiZr passivation and apply it to aluminium components (cast, extruded or formed) to enhance adhesive durability for metal-to-metal bonding and welding.
Powdertech TiZr matches anodising for enhanced adhesive bonding
Extensive testing shows that the stable, protective passivation layer achieved through Powdertech TiZr matches the performance of anodising for durability of adhesive joints.
TiZr pre-treatment has a faster lead time than anodising, uses less energy and is a more cost-effective and environmentally appropriate process than anodising.
Why choose Powdertech TiZr conversion coating?
Automotive OEM specifications
Our TiZr process meets the following Automotive OEM specifications for bonding:
JLR specification STJLR.50.5002B - with Gardobond® X 4591
Tesla specification TS-0002074 - with Gardobond® X 4707
VW/Audi specification TL82428
Morgan specification MMC 1.27
BMW 9702
Gardobond etch passivation techniques and Henkel Bonderite M-NT 2040 give equivalent levels of protection.
Prototype to full production under one roof
We have the capabiity and facilities at our plant to take your project from lab trials to prototype and then to full production. After lab-scale testing ( see equipment details below and on our ‘Our Facility’ page) we run a 7-stage pilot line for prototype part testing and coupon programmes. For full production we have two 14-stage full-sized immersion treatment lines with envelope of 4m x 1.5m x 0.5m.
Laboratory testing with XRF, RFU Spectrometer and Instron equipment
Your products will benefit from ongoing testing that we perform in our Surface Characterisation Laboratory with XRF UV-Florescence equipment and world leading Instron mechanical testing technology. Tests are performed on all the aluminium alloys we work with, from 3xxx series up to 7xxx series, and in all formats. We can test coupons and small test pieces in the early stages of your project.
Individual project advice
Test results enable us to work with you to understand the optimal surface finishing pre-treatment process you need to take bonding strategies to the next level, and to achieve repeatability going forwards. With over twenty years’ experience in TiZr pre-treatment we can advise our clients on a project-by-project basis.
Surface cleanliness
Surface contaminants will impair the performance of any adhesive or coating applied to the metal in terms of bonding performance and also aesthetics. By using XRF equipment Dyne inks and UV-Fluorescence we measure the level of aluminium surface contaminants prior to TiZr passivation.
We will always ensure that your metal is clean before any coating is applied.
Powdertech TiZr Case Studies
The science behind TiZr passivation
For more in depth details we have a range of white papers to read and download:
How Powdertech delivers TiZr conversion coating projects
We carry out a meticulous final inspection - checking dimensions and visual aspects of the parts.
Direct despatch to OEM’s. We are familiar with EDI systems and online booking of transport, direct to end users.
We offer express turnaround in a matter of hours - we are set up for rapid job completion where necessary.
Dedicated warehouse facilities for raw and finished goods.
Discuss TiZr pre-treatment for bonding with us
or find out more about our powder coating services for aluminium and magnesium
More Metal Finishing Services