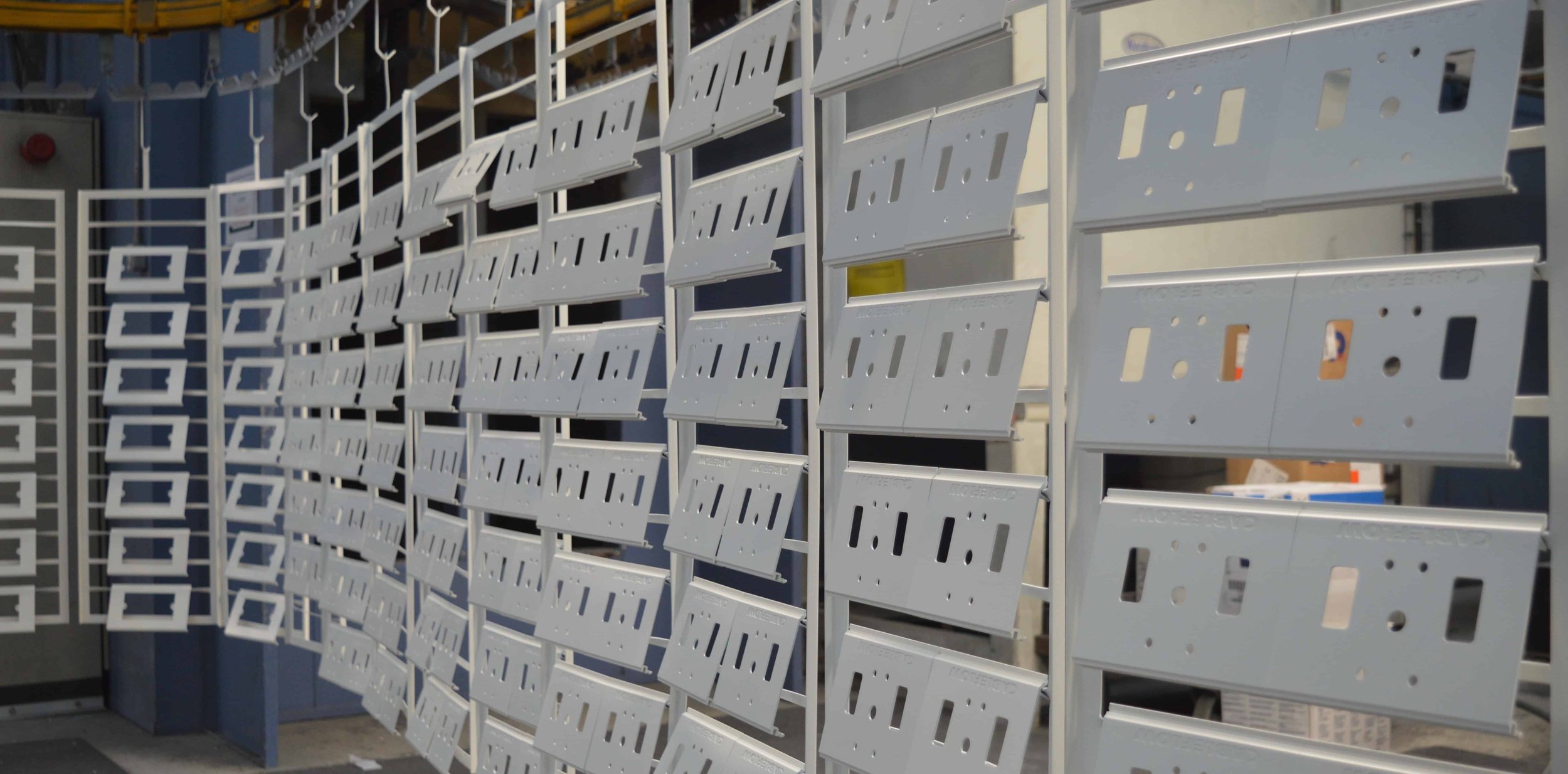
Powder Coating Aluminium
Aluminium surface treatments
Aluminium powder coating and surface treatments for bonding
If you are looking for a dependable powder coating partner who cares about your business outcomes, you are in the right place.
Getting to know you and your products is at the heart of what we do. Through building a close working relationship with you we can be responsive to your business needs – helping you to keep the promises you have made to your customers.
What is powder coating?
The powder is paint in dry powder form, made of resins, binders and pigments. It picks up an electrostatic charge as it leaves the end of a spray gun and becomes attracted to the metal substrate. The coating is then cured by heat to form a smooth hard skin of uniform thickness on the surface of the metal. This is a very different process from wet paint spraying with time saving and control over process variables being big advantages.
Powder coating is a one-coat system and after application the coat can be cured in 20 minutes, whatever the weather.
Benefits of powder coating
The powder coated surface formed by the curing process is a bonded layer with excellent resistance to weather corrosion, scratches, abrasions, chipping and fading.
Being dry, powder coatings have no solvents containing volatile compounds.
Powder coatings are a dry powder and emit zero or negligible volatile organic compounds (VOCs).
Powder coatings contain no halogens or heavy metals.
Powder coatings do not produce hazardous waste. The process takes place in sealed booths and 95% of what is sprayed adheres to the metal or is collected, filtered and re-used. Any powder left over is safely disposed of as an inert powder.
Powder coating takes place in factory-controlled conditions so there is no on-site impact.
Powder coating does not mean ‘end-of life’ status for the metal. The coating can be removed and the metal recycled with no adverse effect.
Automated powder coating booth
Pre-treatment for powder coating
We use only chrome-free pre-treatments in our plant and were the first powder coater in the UK to do so, back in 2001.
We have extensive experience in these safe and effective systems.
Our TiZr chrome-free pre-treatments are eleven-stage Gardobond® X4591 and Gardobond® X 4707 processes. Gardobond etch passivation techniques and Henkel Bonderite M-NT 2040 give equivalent levels of protection.
Our TiZr page gives more detail.
Why choose Powdertech powder coating for aluminium
Your project becomes our focus
You will have our support from design and prototype stage through to full production volumes with a technical, consultative and practical approach.
You will benefit from our experience which covers small complex components to extrusions four metres in length, and specialist tasks such as masking.
We take pride in our work and have a strict quality control regime for pre-treatment and coating systems as you would expect from a Syntha Pulvin® Approved Applicator.
Exceptionally high standards of service
We use high performance powders and the latest automatic powder coating spray equipment to ensure a consistent finish. We regularly invest in new equipment and facilities. Your metal will be pre-treated and coated to an exceptionally high standard and we go beyond that - our expertise extends to developing new pre-treatments and powder coatings for unique applications.
Powder coating plant capacity
You can send us low-volume, fast turnaround prototype parts as well as tightly controlled production components. Our facility can process small, fragile aluminium and magnesium components, as well as accommodating sections up to 4 metres long.
We have a pilot line facility for development work, prototype testing and scale-up validated to two automated production lines.
Chrome-free pre-treatment
Chrome-free since 2001, your project is processed by one of two large automated pre-treatment lines. We use:
Gardobond X4707 ten-stage chrome-free pre-treatment.
Gardobond A4917 phosphate pre-treatment (can also be used for steel).
Iridite NCP. Meeting ELV, RoHS and WEEE standards and qualified under MIL – DTL – 5541 TYPE II CLASS 3 and MIL – DTL – 81706
Aluminium powder coating case studies
Typical items we coat include automotive components, medical trunking, medical equipment, aircraft interiors and light fittings.
How Powdertech delivers aluminium powder coating projects
We carry out a meticulous final inspection - checking dimensions and visual aspects of the parts.
Direct despatch to OEM’s. We are familiar with EDI systems and online booking of transport, direct to end users.
We offer express turnaround in a matter of hours - we are set up for rapid job completion where necessary.
Dedicated warehouse facilities for raw and finished goods.
More Metal Finishing Services