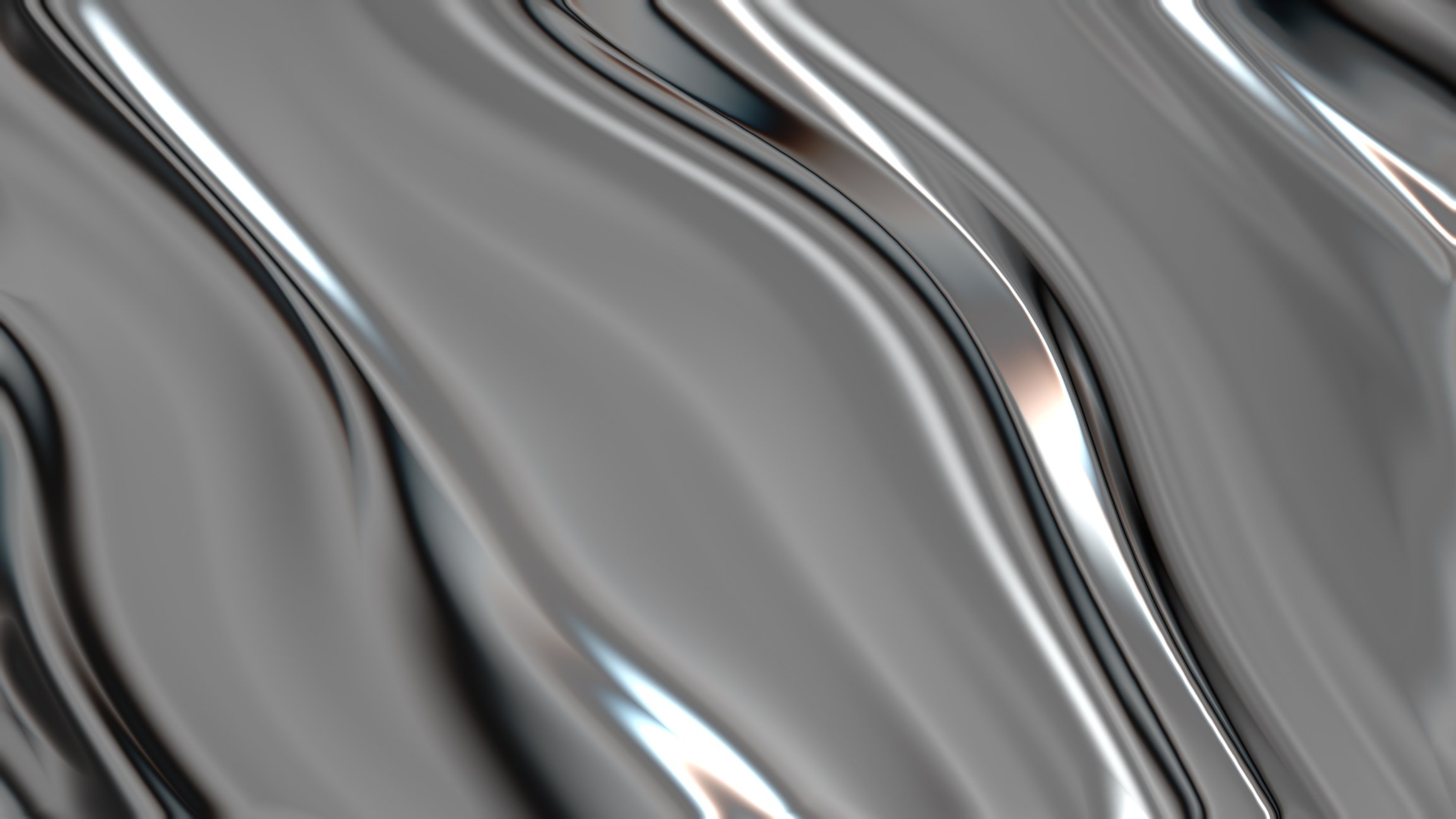
Powder Coating Magnesium
Magnesium Surface Treatments
Magnesium powder coating and surface treatments
We have over a decade of experience in processing magnesium, used extensively in the automotive, electric vehicle, aerospace and bio-medical industries. As light weighting becomes ever more crucial in markets with strict emission targets, die-cast magnesium alloys are being used for light-weight structures to reduce weight yet further without compromising overall strength.
Magnesium also has a vibration damping capacity which is beneficial in applications where the internal forces of high-speed components need to be reduced. For electronic devices magnesium alloys are often chosen as they can dissipate heat and shield against (EMI) electromagnetic interference.
Magnesium is a highly reactive metal and also only forms a weak natural oxide layer on exposure at room temperature. This makes it particularly susceptible to corrosion, meaning that careful cleaning, suitable pre-treatments and edge to edge final coating are imperative.
Powder coating and its benefits
The powder is paint in dry powder form, made of resins, binders and pigments. It picks up an electrostatic charge as it leaves the end of a spray gun and becomes attracted to the metal substrate. The coating is then cured by heat to form a smooth hard skin of uniform thickness on the surface of the metal. Powder coating is a one-coat system and after application the coat can be cured in 20 minutes.
The powder coated surface formed by the curing process is a bonded layer with excellent resistance to weather corrosion, scratches, abrasions, chipping and fading. Being dry, powder coatings have no solvents containing volatile compounds.
Powder coatings are a dry powder and emit zero or negligible volatile organic compounds (VOCs).
Powder coatings contain no halogens or heavy metals.
Powder coating does not mean ‘end-of life’ status for the metal. The coating can be removed and the metal recycled with no adverse effect.
Pre-treatment for magnesium
We use only chrome-free pre-treatments in our plant and were the first powder coater in the UK to do so, back in 2001.
We have extensive experience in these safe and effective systems.
Automotive: We operate all large automotive OEM approved magnesium chrome-free pre-treatment systems.
Aerospace: Gardobond X4729 eleven-stage chrome-free pre-treatment (also known as Ardrox 1769) is used for aerospace-approved magnesium alloys to class L (with top coat) or class S (no top coat) specification.
Why choose Powdertech powder coating for magnesium
We have 10+ years of experience
We have coated magnesium components for our clients for over a decade and therefore have extensive experience in handling this metal.
Investment in equipment and surface treatments
You can rely on our high performance pre-treatments specifically designed for magnesium alloys and the latest automatic powder coating technology to ensure consistent coverage.
We specialise in complex and demanding components
From small electronics housings to large high pressure die castings
We work with you as a partner throughout the project.
You require a partner who will support you from design and prototype stage through to full production volumes. Our technical and consultative approach is there to assist you through this process. We believe that dependability and reliability form the basis of our relationship. We work hard to get to know you and your products so that you can trust us to deliver on your behalf.
Dependable, accredited powder coating supplier
You can rely on us to provide you with the quality that you would expect from a Syntha Pulvin® Approved Applicator. We run a strict quality control regime, both with pre-treatment and coating systems
Magnesium surface treatment case study
Typical items we powder coat include front end carriers (FECs), grille opening reinforcements (GOR), rear lift gates, medical components and aircraft seating.
How Powdertech delivers magnesium powder coating projects
We carry out a meticulous final inspection - checking dimensions and visual aspects of the parts.
Direct despatch to OEM’s. We are familiar with EDI systems and online booking of transport, direct to end users.
We offer express turnaround in a matter of hours - we are set up for rapid job completion where necessary.
Dedicated warehouse facilities for raw and finished goods.
Discuss your magnesium powder coating requirements with us
or find out more about our powder coating services for aluminium and INTRICOAT
More Metal Finishing Services